If you’re looking to create a plastic prototype of a functional component, especially for a product or a part that includes a functional aspect such as electronics integration, moving parts, or specific material properties, here are the general steps and considerations involved:
Steps to Develop a Plastic Prototype for a Functional Component:
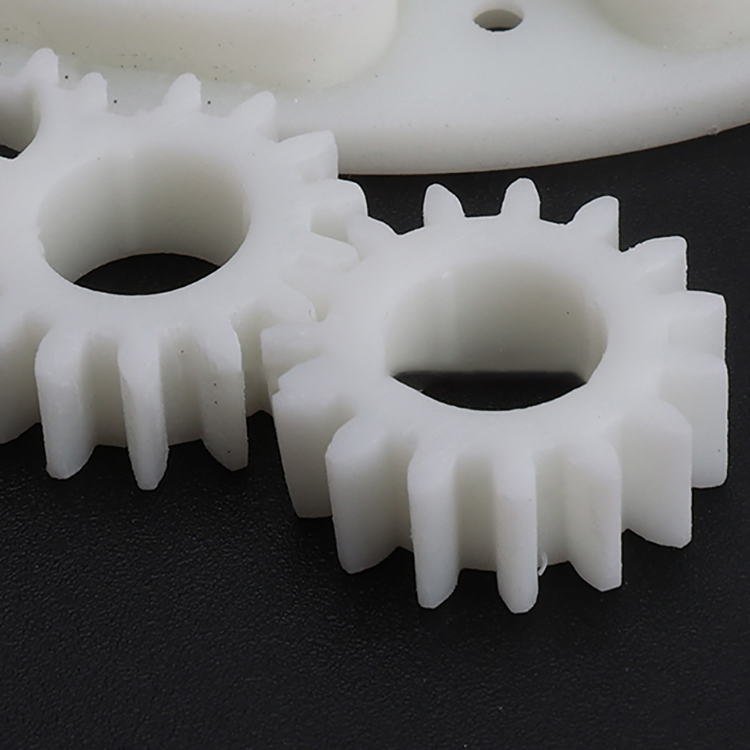
1.Conceptualization and Design:
2.Define Requirements: Clearly outline the functionality, dimensions, and material requirements for your functional component.
3.Concept Development: Sketch or use CAD software to create conceptual designs. Consider ergonomics, aesthetics, and functional aspects.
4.Detailed Design:
5.CAD Modeling: Create detailed 3D models using CAD software (e.g., SolidWorks, Autodesk Inventor) based on your conceptual design.
6.Design Validation: Perform simulations or virtual testing to validate the design’s functionality and identify potential issues.
7.Material Selection:
8.Choose appropriate plastic materials based on mechanical properties (e.g., strength, flexibility), environmental factors (e.g., temperature resistance), and manufacturing feasibility (e.g., moldability).
9.Prototype Fabrication:
10.3D Printing: Use rapid prototyping techniques like FDM (Fused Deposition Modeling) or SLA (Stereolithography) to create plastic prototypes directly from CAD models.
11.CNC Machining: For more robust prototypes, CNC machining can be used to produce parts from solid blocks of plastic.
12.Assembly and Integration:
13.Assemble the functional components into the prototype using appropriate fasteners, adhesives, or integration techniques.
14.Integrate electronics, sensors, or other functional elements as required by the design.
15.Testing and Iteration:
16.Conduct functional testing to ensure the prototype performs as expected under simulated conditions.
17.Gather feedback from stakeholders and iterate on the design based on testing results and user feedback.
18.Documentation:
19.Prepare documentation including assembly instructions, materials used, and any design considerations for future reference and production scaling.
20.Production Preparation:
21.Once the prototype is finalized and tested, prepare for full-scale production by refining manufacturing processes and preparing tooling if necessary.
Considerations:
22.Functional Requirements: Ensure that the prototype meets all functional specifications and performs reliably under expected conditions.
23.Material Properties: Select plastic materials that offer the necessary mechanical and environmental properties for your application.
24.Manufacturability: Consider the chosen manufacturing method (e.g., 3D printing, CNC machining) and its impact on design complexity and cost.
25.Testing: Rigorously test the prototype to identify and address any design flaws or performance issues early in the development process.
26.Cost and Time: Evaluate the cost-effectiveness and time constraints associated with different prototyping methods and materials.
By following these steps and considerations, you can effectively develop a plastic prototype of a functional component that meets your design requirements and prepares you for further development or production.