CNC Aluminum Parts and Aluminum CNC Milling Parts: An In-Depth Exploration
Introduction
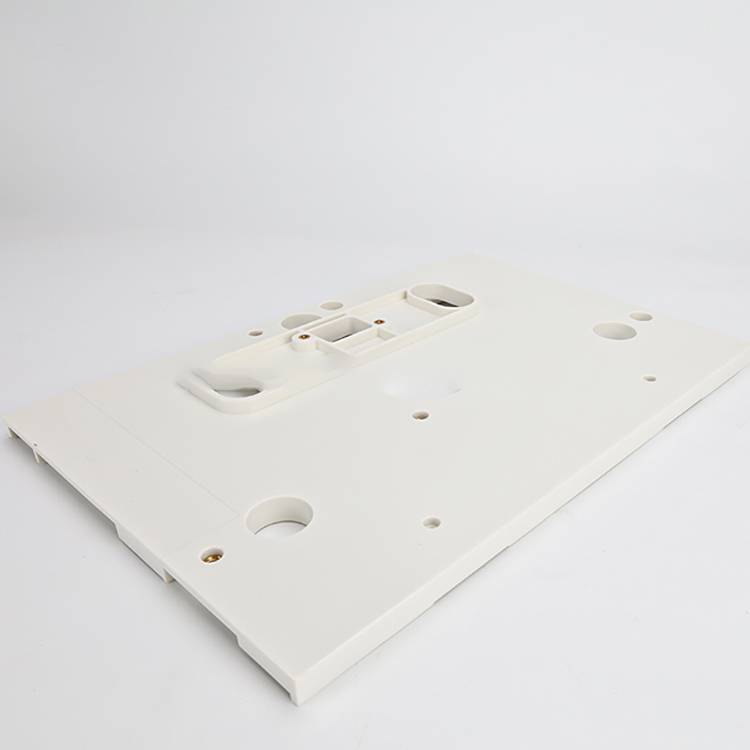
1. Characteristics of Aluminum and CNC Machining
1.1 Aluminum Material Properties
Aluminum is renowned for its combination of properties that make it ideal for various applications:
Lightweight: With a density approximately one-third that of steel, aluminum is ideal for applications where weight reduction is critical.
Strength and Durability: Aluminum alloys can be strengthened to provide high tensile strength and resistance to wear.
Corrosion Resistance: Aluminum naturally forms a protective oxide layer that makes it highly resistant to corrosion.
Excellent Machinability: Aluminum is relatively soft and easy to machine, which allows for intricate and complex designs.
1.2 CNC Machining Technology
CNC machining refers to the use of computer-controlled machine tools to perform various operations such as cutting, drilling, and milling. This technology enables:
Precision: CNC machines can achieve high levels of accuracy, down to micrometers.
Consistency: CNC ensures that each part produced conforms precisely to the design specifications.
Complexity: CNC can handle complex geometries and detailed designs that would be difficult to achieve with manual machining.
2. CNC Aluminum Parts: Manufacturing Processes
2.1 Types of CNC Machining for Aluminum
Several CNC machining processes are used to fabricate aluminum parts, including:
Milling: The process involves removing material from a workpiece using rotary cutters. CNC milling can produce various shapes and features, such as slots, pockets, and complex contours.
Turning: In this process, a rotating workpiece is cut with a stationary tool to create cylindrical parts. CNC turning is suitable for creating parts with symmetrical shapes.
Drilling: CNC drilling machines create holes in aluminum parts with high precision. This process is often used in conjunction with milling operations.
Grinding: For finishing operations, CNC grinding machines achieve fine tolerances and surface finishes.
2.2 Key Parameters in CNC Aluminum Milling
Effective CNC milling requires careful consideration of several parameters:
Cutting Speed: This is the speed at which the cutting tool engages the aluminum. Higher speeds are typically used for aluminum due to its favorable thermal properties.
Feed Rate: This is the speed at which the workpiece or tool advances through the material. Optimal feed rates balance material removal rates and tool wear.
Depth of Cut: This refers to the thickness of the material removed in a single pass. Adjusting the depth of cut affects the machining time and surface finish.
2.3 Tool Selection for CNC Aluminum Milling
Choosing the right tools is crucial for efficient and effective CNC milling of aluminum:
Carbide Tools: These tools are highly durable and capable of withstanding high cutting speeds, making them suitable for aluminum alloys.
Coated Tools: Tools with coatings, such as TiAlN (Titanium Aluminum Nitride), offer improved performance by reducing friction and enhancing heat resistance.
3. Applications of CNC Aluminum Parts
3.1 Aerospace Industry
The aerospace sector relies heavily on aluminum due to its lightweight and high-strength properties. CNC aluminum parts are used in:
Aircraft Structures: Fuselages, wing components, and landing gear assemblies.
Engine Components: Parts like brackets, housings, and covers that require high precision and strength.
3.2 Automotive Industry
Aluminum parts play a critical role in the automotive industry:
Engine Components: Cylinder heads, pistons, and engine blocks are often made from aluminum to reduce weight and improve performance.
Body Panels: Aluminum is used in car body panels and frames to enhance fuel efficiency and safety.
3.3 Electronics Industry
In the electronics sector, aluminum is used for:
Heat Sinks: To dissipate heat from electronic components, ensuring efficient operation and longevity.
Enclosures: Protective housings for sensitive electronic equipment.
3.4 Medical Devices
CNC aluminum parts are also used in medical technology:
Surgical Instruments: Precision components such as handles and casings for surgical tools.
Diagnostic Equipment: Parts for imaging devices and other diagnostic machinery.
4. Advantages and Challenges of CNC Aluminum Parts
4.1 Advantages
High Precision and Accuracy: CNC machining provides exceptional precision, which is crucial for complex and high-tolerance parts.
Flexibility: CNC machines can produce a wide range of shapes and sizes, accommodating custom designs and rapid prototyping.
Efficiency: Automated CNC processes reduce manual labor and production time, improving overall efficiency.
4.2 Challenges
Cost: High-quality CNC machines and tooling represent a significant investment, which can be a barrier for smaller operations.
Material Considerations: Although aluminum is easy to machine, its thermal conductivity requires careful management of cutting temperatures to avoid issues like thermal expansion or warping.
Tool Wear: The high-speed machining of aluminum can lead to increased tool wear, necessitating regular maintenance and tool changes.
5. Future Trends in CNC Aluminum Machining
5.1 Technological Advancements
Future developments in CNC technology will focus on:
Automation: Enhanced automation through robotics and AI will further improve efficiency and reduce human error.
Smart Machines: Integration of IoT (Internet of Things) will allow machines to self-monitor and optimize performance in real-time.
5.2 New Materials and Processes
Advanced Aluminum Alloys: New aluminum alloys with improved properties will expand the range of applications and performance capabilities.
Additive Manufacturing: Combining CNC machining with additive manufacturing techniques, such as 3D printing, will enable more complex and customized designs.
5.3 Sustainable Practices
Energy Efficiency: Efforts to reduce the energy consumption of CNC machines and processes will align with global sustainability goals.
Recycling: Increased focus on recycling aluminum and minimizing waste will contribute to more eco-friendly manufacturing practices.