It sounds like you’re interested in manufacturing custom plastic parts with a small minimum production requirement. Here’s a breakdown of how this typically works:
Custom Plastic Parts Manufacturing:
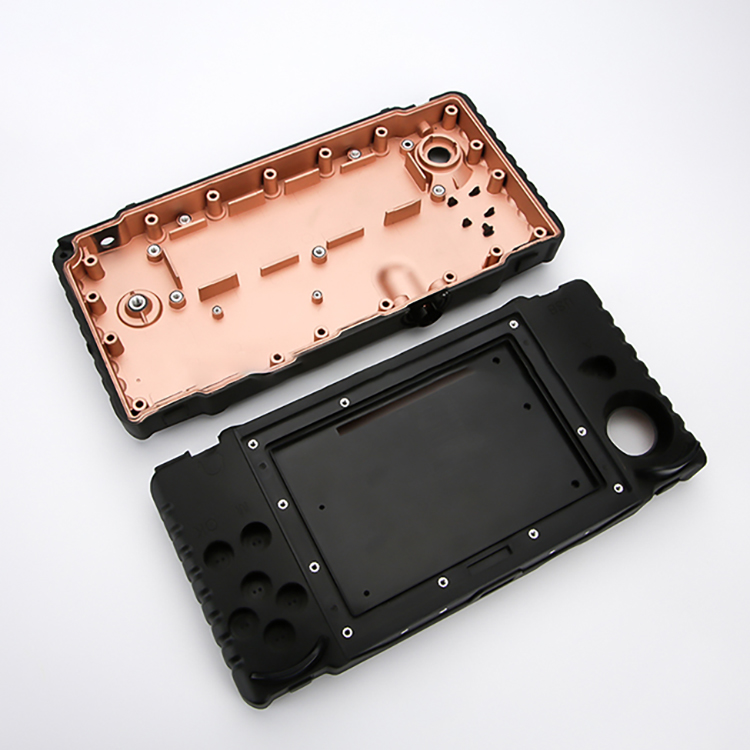
1.Design Phase:
2.CAD Design: Your custom plastic part design starts with a Computer-Aided Design (CAD) file. This file defines the dimensions, features, and specifications of the part.
3.Prototype: Before production, it’s common to create a prototype to verify the design and functionality. This can be done through 3D printing or other rapid prototyping methods.
4.Manufacturing Options:
5.Injection Molding: This is the most common method for manufacturing plastic parts in large volumes. However, it typically requires higher initial costs due to mold creation.
6.CNC Machining: For small volumes or complex designs, CNC machining can be a viable option. It involves cutting away material from a block of plastic to create the desired shape.
7.3D Printing: Suitable for rapid prototyping and small production runs. It’s ideal for complex geometries and quick turnaround times.
8.Vacuum Forming: Used for producing thin-walled, large plastic parts with lower tooling costs compared to injection molding.
manufacture process | advantage |
Vacuum Forming | large plastic parts with lower tooling costs |
9.Minimum Order Quantity (MOQ):
10.Injection Molding: MOQs are typically higher due to setup costs associated with creating molds. They can range from hundreds to thousands of units depending on the complexity and size of the part.
11.CNC Machining: Often suitable for low-volume production with no strict MOQ, making it cost-effective for small batches.
12.3D Printing: No strict MOQ; parts can be produced on-demand, making it ideal for small quantities.
13.Vacuum Forming: MOQs can vary but generally lower compared to injection molding, depending on the size and complexity of the part.
14.Choosing a Manufacturer:
15.Look for manufacturers or prototyping services that specialize in small-batch or custom production.
16.Ensure they have experience with the specific plastic material you require (e.g., ABS, polypropylene, polycarbonate).
17.Check their capabilities, including equipment, quality control measures, and ability to meet your timeline and budget.
18.Cost Considerations:
19.Initial setup costs (e.g., mold creation for injection molding) can be significant but are spread across the production run.
20.Unit costs for small batches are typically higher due to setup and labor costs.
21.3D printing can offer cost-effective solutions for small quantities initially, with options to scale as needed.
When looking to produce custom plastic parts with a small minimum requirement, consider the complexity of your design, material specifications, budget, and timeline. Each manufacturing method has its strengths and limitations, so choosing the right approach depends on your specific needs and priorities.