When working with CNC machining for small aluminum parts, several key considerations and processes come into play. Here’s a comprehensive overview:
CNC Machining for Small Aluminum Parts
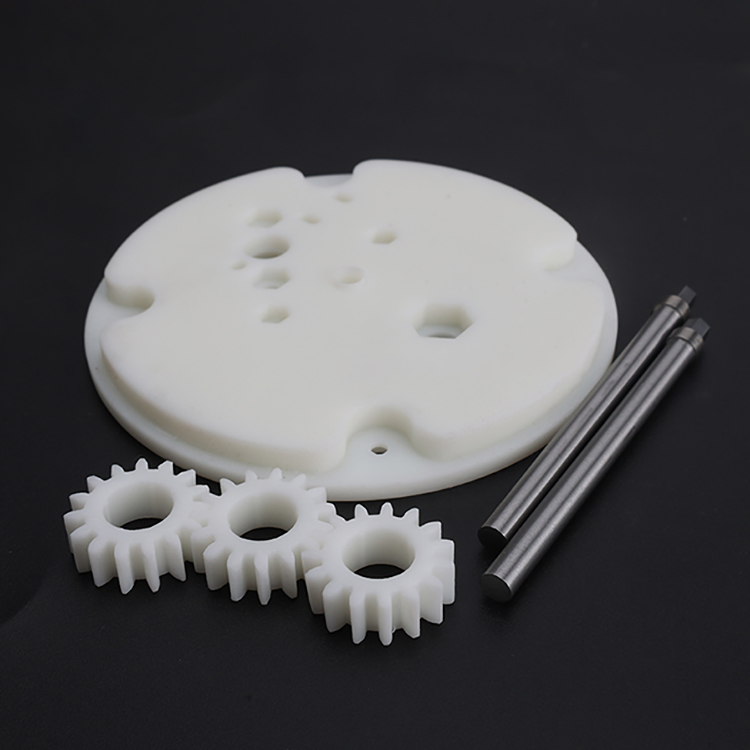
1. Understanding CNC Machining:
1)CNC Machining: Computer Numerical Control (CNC) machining uses pre-programmed software to control the movement of machinery and tools, allowing for precise cutting, drilling, milling, and turning of materials.
2)Materials: Aluminum is a popular choice due to its lightweight, durability, and machinability.
2. Benefits of CNC Machining for Aluminum Parts:
1)Precision: CNC machines provide high accuracy and repeatability, essential for small parts.
2)Complexity: Capable of producing intricate shapes and detailed features.
3)Consistency: Ensures uniformity across multiple parts, which is crucial for applications requiring tight tolerances.
3. Design Considerations:
1)Tolerance and Dimensions: Define the exact dimensions and tolerances needed for your parts. Aluminum’s machinability allows for tight tolerances, but ensure your design accounts for this.
2)Draft Angles: Include draft angles if parts will be cast or require ejection from molds.
3)Wall Thickness: Maintain a consistent wall thickness to avoid weak spots and ensure structural integrity.
4)Heat Dissipation: Consider heat dissipation if your parts will be used in high-temperature environments.
4. Choosing the Right Aluminum Alloy:
1)6061: Commonly used for its good mechanical properties and resistance to corrosion.
2)7075: Offers higher strength but is more challenging to machine.
3)2024: Known for its high strength but is less corrosion-resistant.
5. CNC Machining Process:
1)CAD Design: Start with a detailed CAD (Computer-Aided Design) model of your parts. Tools like SolidWorks or Fusion 360 are popular choices.
2)CAM Programming: Convert the CAD model into a CAM (Computer-Aided Manufacturing) program. This involves defining tool paths and machining strategies.
3)Machine Setup: Load the aluminum stock into the CNC machine. Ensure proper fixturing to secure the part during machining.
4)Machining: Execute the machining process according to the CAM program. This includes milling, turning, drilling, or other operations as required.
5)Finishing: After machining, parts may require additional finishing processes like anodizing, painting, or polishing.
6. Quality Control:
1)Inspection: Use precision measurement tools such as calipers, micrometers, or CMMs (Coordinate Measuring Machines) to check dimensions and tolerances.
2)Testing: Perform functional testing if applicable to ensure parts meet performance requirements.
7. Rapid Prototyping:
1)Low Volume Production: CNC machining is ideal for small-batch production or prototyping. It allows you to quickly iterate and refine designs before mass production.
2)Cost Efficiency: Although initial setup may be costly, CNC machining can be cost-effective for small quantities due to its efficiency and precision.
8. Finding a CNC Machining Service:
1)Local Shops: Look for local CNC machining services that offer small-part production. They can often provide quick turnaround times.
2)Specialized Providers: Some companies specialize in aluminum CNC machining and offer additional services like design consultation and finishing.
Summary
CNC machining is an excellent method for producing small aluminum parts due to its precision and versatility. By carefully considering design, material choice, and machining processes, you can achieve high-quality components suitable for a wide range of applications. Whether for prototyping or small-batch production, leveraging CNC machining effectively ensures that your aluminum parts meet both design specifications and functional requirements.