ABS injection molding is commonly used to manufacture plastic parts for various applications, including car mount holders. ABS (Acrylonitrile Butadiene Styrene) is chosen for its strength, impact resistance, and affordability, making it suitable for products that require durability and a smooth finish.
When producing ABS plastic parts for car mount holders through injection molding, manufacturers typically follow these steps:
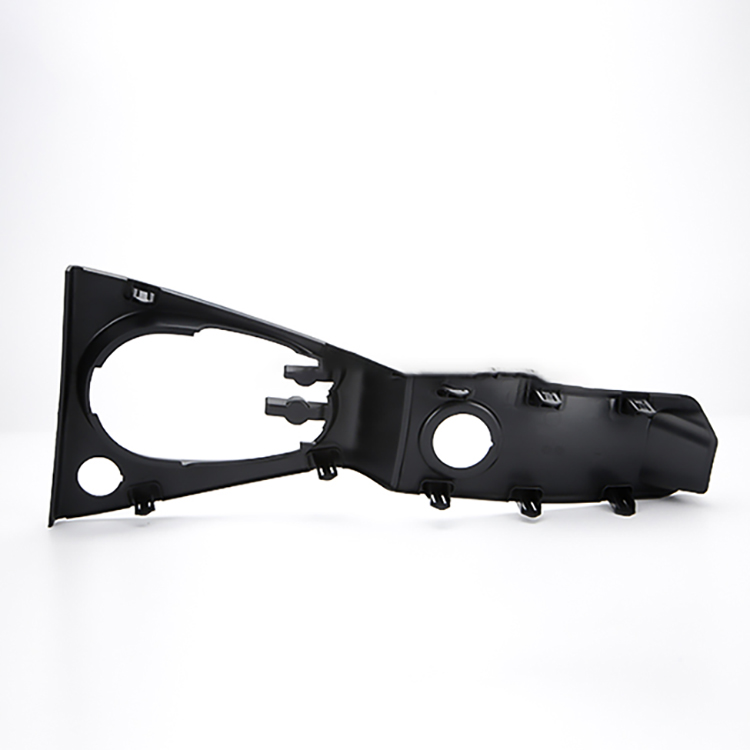
1.Design and CAD Development: Engineers create a detailed CAD (Computer-Aided Design) model of the car mount holder, ensuring it meets functional and aesthetic requirements.
2.Tooling and Mold Design: A mold is designed based on the CAD model. This mold will shape the molten ABS into the desired form during the injection molding process.
3.Material Selection: ABS resin pellets are selected based on the specific properties needed, such as color, UV resistance, or fire retardancy.
4.Injection Molding Process:
5.Preparation: ABS pellets are loaded into the hopper of the injection molding machine.
6.Heating and Melting: The pellets are heated and melted inside a barrel, where they reach a molten state.
7.Injection: The molten ABS is injected under pressure into the mold cavity, which is the inverse of the car mount holder’s shape.
8.Cooling: The mold is cooled to solidify the ABS into the desired shape.
9.Ejection: Once cooled, the mold opens, and the newly formed ABS part (car mount holder) is ejected.
10.Finishing: Depending on the design requirements, additional processes such as trimming excess material, surface finishing (like polishing or painting), and assembly may be performed.
11.Quality Control: Throughout the manufacturing process, quality checks ensure that each ABS part meets dimensional accuracy, strength, and appearance standards.
12.Packaging and Shipping: Finished ABS parts are packaged according to customer specifications and shipped for assembly or distribution.
For car mount holders, ABS plastic offers benefits such as resistance to heat and impact, which are essential for holding electronic devices securely in vehicles. The injection molding process allows for efficient production of these parts in large quantities, meeting automotive industry standards for performance and reliability.