A custom plastic injection molding service typically involves several key steps and processes to deliver high-quality, tailored plastic parts to clients. Here’s a general overview:
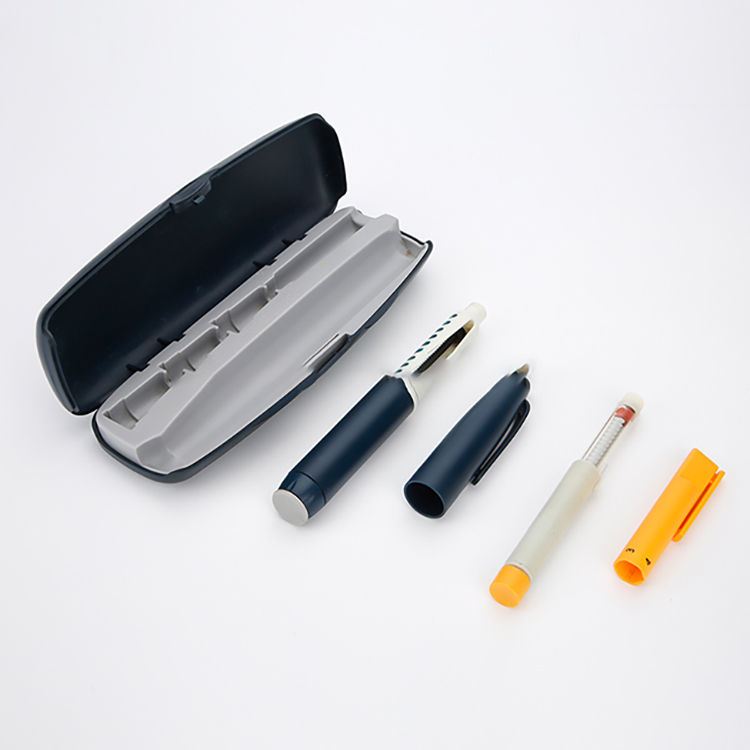
1.Requirement Gathering and Design: The process begins with understanding the client’s requirements, including part specifications, desired materials, quantity, and any special considerations. This may involve collaboration between the client and the molding service provider to refine the design and optimize manufacturability.
2.Tooling Design and Fabrication: Once the part design is finalized, molds (also known as tools) are designed and fabricated. This involves CNC machining or other manufacturing processes to create precise molds that will shape the molten plastic into the desired part geometry.
3.Material Selection: Choosing the right plastic material is crucial for meeting the part’s performance requirements. Factors such as mechanical properties, chemical resistance, temperature resistance, and cost are considered during material selection.
4.Injection Molding Process Setup: The injection molding machine is set up and prepared for production. This includes heating the plastic resin to its melting point and injecting it into the mold cavity under high pressure.
5.Injection Molding: Molten plastic material is injected into the mold cavity, where it takes the shape of the mold. The mold is held closed under pressure until the plastic cools and solidifies.
6.Cooling and Ejection: After the plastic has cooled and solidified, the mold opens, and the finished part is ejected. Cooling time is critical to ensure proper part quality and cycle time efficiency.
7.Quality Control: The molded parts undergo rigorous quality inspection to ensure they meet the specified requirements and standards. This may involve dimensional checks, visual inspection, mechanical testing, and other quality assurance measures.
8.Secondary Operations (if needed): Depending on the client’s requirements, additional secondary operations may be performed, such as trimming, machining, assembly, surface finishing, or packaging.
9.Delivery and Support: Once the parts pass quality inspection, they are packaged and delivered to the client. The molding service provider may also offer ongoing support, including reorders, design improvements, and technical assistance.
Throughout the entire process, communication and collaboration between the client and the molding service provider are crucial to ensure that the final parts meet expectations in terms of quality, functionality, and cost-effectiveness.