Producing ABS injection molded plastic parts for low-volume production involves several considerations and steps to ensure quality and cost-effectiveness. Here’s a structured approach:
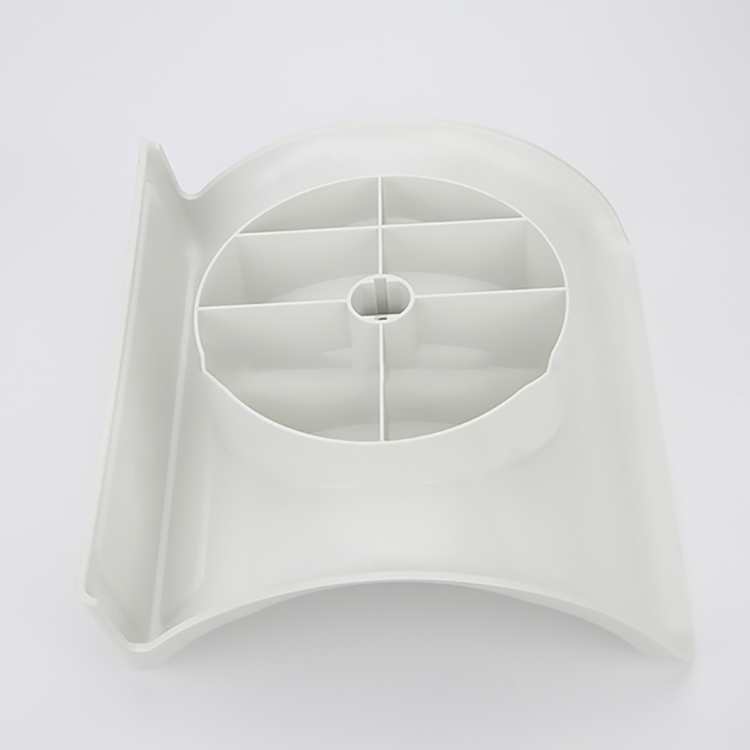
- Design and Prototyping
(1).Design Preparation: Start with detailed CAD designs optimized for injection molding. Ensure designs consider draft angles, wall thickness, and part geometry suitable for ABS.
(2).Prototype Development: Create prototypes using rapid prototyping methods like 3D printing or CNC machining to validate design concepts and functional requirements before committing to injection molds.
- Material Selection
ABS Material Choice: Select ABS resin suitable for injection molding, considering factors like strength, impact resistance, temperature stability, and surface finish requirements.
- Tooling and Mold Design
(1) Tooling Options: For low volumes, consider aluminum molds which are cost-effective and faster to produce than steel molds but may have shorter lifespan. Steel molds are more durable but expensive.
(2) Mold Design Considerations: Optimize mold design for easy ejection, minimal shrinkage, and consistent part quality. Ensure gates, runners, and cooling channels are well-designed for efficient molding.
- Injection Molding Process
(1) Setup and Injection: Setup injection molding machines to the specified parameters for ABS. Monitor and adjust settings for temperature, pressure, and cycle times to achieve quality parts.
(2) Quality Control: Implement inspection procedures to monitor part dimensions, cosmetic defects, and material properties. Address any issues early to maintain consistency.
- Post-Molding Operations
Part Finishing: Perform secondary operations like trimming, deburring, and surface finishing to meet final specifications and aesthetic requirements.
- Assembly and Packaging
(1) Assembly: If required, assemble components into sub-assemblies or finished products. Ensure parts fit together correctly and function as intended.
(2) Packaging: Package parts securely to prevent damage during shipping and storage, considering customer requirements and logistics.
- Testing and Validation
(1).Functional Testing: Conduct functional tests to ensure parts meet performance requirements under simulated conditions.
(2).Feedback and Iteration: Gather feedback from testing and make necessary design or process adjustments for continuous improvement.
- Documentation and Compliance
(1) Documentation: Maintain comprehensive records of production processes, quality inspections, and material certifications for traceability and compliance.
(2) Considerations for Low-Volume Production:
(3) Cost Efficiency: Balance tooling costs with production volume and part complexity to optimize cost-effectiveness.
(4) Flexibility: Injection molding allows for scalability in production quantities, adjusting volumes based on demand fluctuations.
(5) Lead Times: Plan lead times considering mold fabrication, production setup, and testing phases to meet project timelines.
By following these steps and considerations, you can effectively manage the production of ABS injection molded plastic parts for low-volume production, ensuring both quality and cost-efficiency throughout the process.