ABS (Acrylonitrile Butadiene Styrene) injection molding is commonly used for producing plastic parts, including car mount holders. Here are some key points regarding ABS injection molded parts for car mount holders:
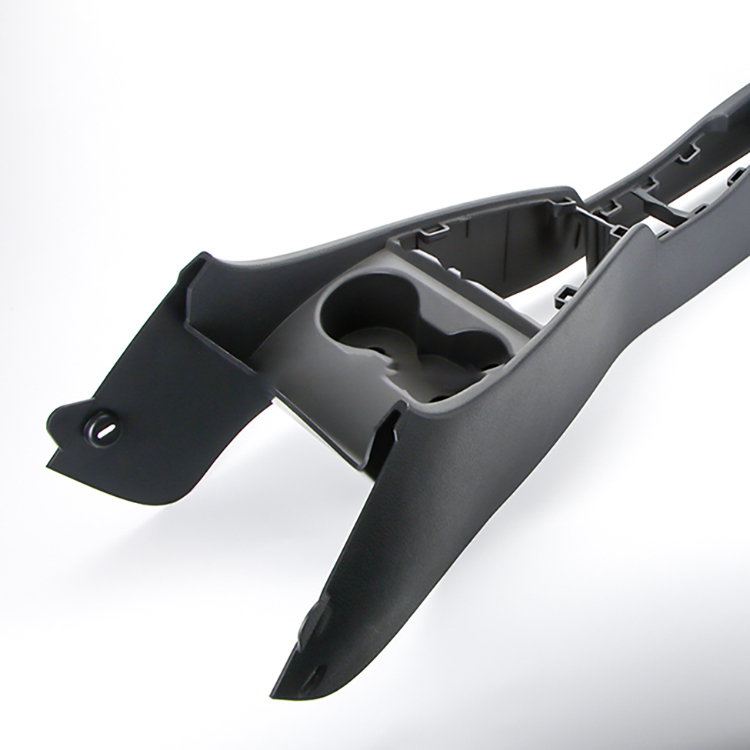
1.Material Characteristics:
2.Strength: ABS offers good strength and rigidity, making it suitable for parts that need to withstand mechanical stresses, such as those in car mount holders.
3.Impact Resistance: It has excellent impact resistance, which is crucial for automotive applications where parts may be subject to vibrations and shocks.
4.Heat Resistance: ABS can withstand moderate temperatures, which is important for parts exposed to varying conditions inside a vehicle.
5.Surface Finish: ABS can be easily polished and textured, providing a smooth and aesthetically pleasing surface finish.
6.Design Flexibility:
7.ABS injection molding allows for complex geometries and detailed features, which is beneficial for designing custom car mount holders that fit specific device sizes and shapes.
8.It supports the integration of features like clips, hooks, and adjustable joints directly into the part design.
9.Durability and Longevity:
10.ABS parts are durable and resistant to wear and tear, ensuring longevity even with frequent use in automotive environments.
11.The material retains its properties over time, maintaining functionality and appearance of car mount holders.
12.Manufacturing Process:
13.Injection molding is a highly efficient manufacturing process for ABS parts, enabling high-volume production with consistent quality.
14.It allows for rapid production cycles, which is advantageous for meeting market demands and iterating designs based on user feedback.
15.Customization and Branding:
16.ABS parts can be easily customized with colors, surface textures, and logos, allowing car mount holders to align with branding and design preferences.
When selecting ABS injection molded plastic parts for car mount holders, it’s essential to work with a manufacturer or supplier who understands automotive requirements and can provide prototypes for testing and validation. This ensures that the final parts meet performance standards and customer expectations in terms of durability, functionality, and aesthetic appeal.