Rapid prototyping is a crucial process in product development, enabling designers and engineers to quickly iterate and refine their concepts. When it comes to creating aluminum prototypes, precision and speed are key. Here, we explore the most effective methods for producing aluminum prototypes, focusing on rapid and controlled techniques that ensure high-quality outcomes.
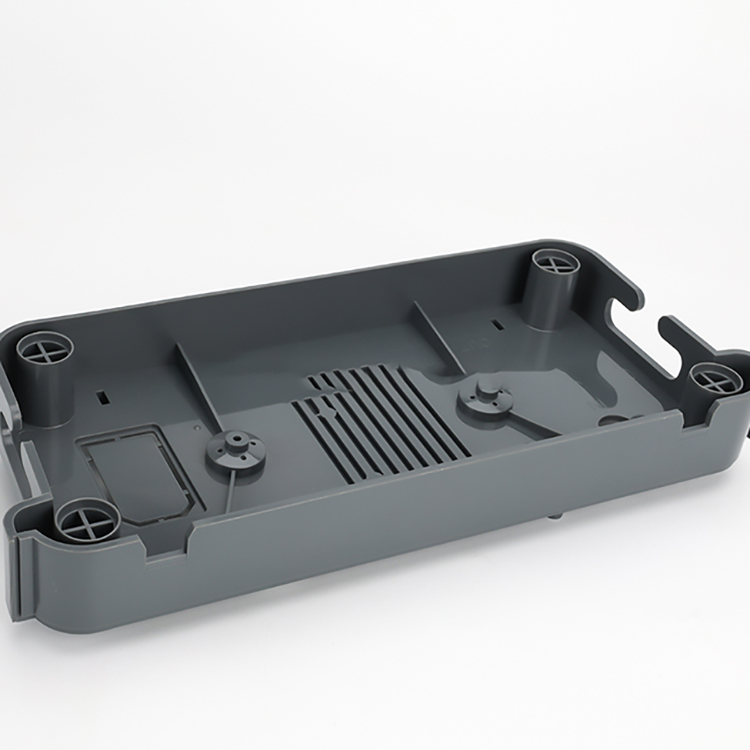
Table of Contents
1. CNC Machining
Overview: CNC (Computer Numerical Control) machining is a highly precise manufacturing process where a computer-controlled machine cuts, drills, or mills aluminum to create a prototype. This method is widely used due to its accuracy and the quality of the final product.
Advantages:
- High Precision: CNC machines can achieve tight tolerances, ensuring that prototypes closely match the design specifications.
- Surface Finish: Provides a high-quality surface finish suitable for functional testing and aesthetic evaluations.
- Material Versatility: CNC machining works well with various aluminum alloys, offering flexibility in material properties.
Applications: CNC machining is ideal for producing complex geometries and detailed parts, making it suitable for applications that require intricate designs or functional components.
Limitations:
- Lead Time: While faster than traditional methods, CNC machining may not be as rapid as other prototyping techniques.
- Cost: The setup and material costs can be relatively high, especially for small production runs.
2. 3D Printing (Additive Manufacturing)
Overview: 3D printing, specifically Selective Laser Melting (SLM) or Direct Metal Laser Sintering (DMLS), uses a laser to melt and fuse aluminum powder into precise layers to build up a prototype. This process is part of additive manufacturing, where material is added layer by layer.
Advantages:
- Rapid Turnaround: 3D printing allows for quick production of prototypes directly from digital models, reducing lead times.
- Complex Geometries: Capable of producing complex and intricate designs that may be difficult or impossible with traditional methods.
- Material Efficiency: Minimizes waste by adding material only where needed.
Applications: 3D printing is excellent for prototypes requiring complex internal structures or unique geometrical features. It’s also useful for creating parts for functional testing or low-volume production runs.
Limitations:
- Surface Finish: Parts may require additional finishing to achieve a smooth surface.
- Material Strength: Although advances are being made, 3D-printed aluminum parts may not always match the mechanical properties of traditionally machined components.