When discussing plastic mould companies and the steel used in plastic moulding, it’s essential to understand the critical role that both play in the manufacturing process. Here’s a detailed look into both aspects:
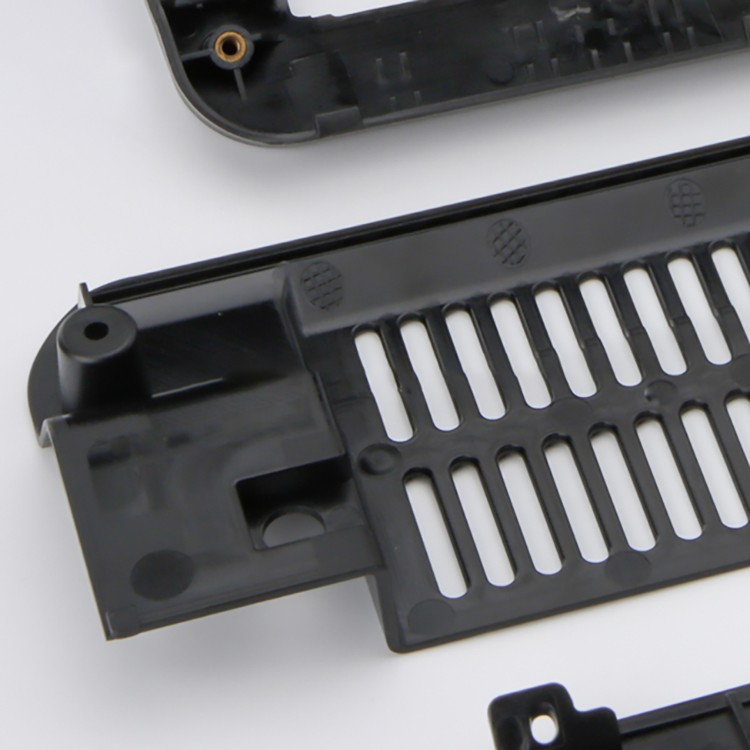
Plastic Mould Companies
Plastic mould companies specialize in designing, manufacturing, and maintaining moulds used in the injection moulding process. These companies provide crucial services for various industries, including automotive, consumer goods, electronics, and medical devices. The core functions of such companies include:
Design and Engineering:
Custom Mould Design: Tailoring moulds to specific product requirements, often using CAD software for precision.
Prototype Development: Creating prototypes to test design viability before full-scale production.
Mould Manufacturing:
Tooling: Fabrication of moulds using various methods, including CNC machining and EDM (Electrical Discharge Machining).
Material Selection: Choosing the right materials for the mould based on the type of plastic used and the intended lifespan of the mould.
Testing and Quality Control:
Trial Runs: Conducting trial runs to ensure the mould functions correctly and produces parts to specification.
Inspection: Performing rigorous inspections to guarantee that the mould meets all quality and safety standards.
Maintenance and Repair:
Regular Maintenance: Ensuring the mould remains in good condition throughout its service life.
Repairs and Upgrades: Addressing issues that arise and making necessary upgrades to improve performance or extend the mould’s life.
Plastic Mould Steel
The steel used in plastic moulds is crucial because it directly impacts the mould’s performance, durability, and the quality of the final product. Several types of steel are used, each suited to different requirements:
Types of Steel:
P20 Steel: Commonly used for making moulds for large production runs. It has good machinability and is often used for intermediate applications.
H13 Steel: Known for its high resistance to heat and wear. It’s suitable for moulds that will be exposed to high temperatures and abrasive materials.
S7 Steel: Provides excellent toughness and shock resistance, often used for tools that endure heavy use and impact.
718 Steel: Offers a good balance of hardness and machinability. It’s frequently used for complex and high-precision moulds.
Steel Properties:
Hardness: Steel must be hard enough to withstand the forces involved in moulding without deforming.
Toughness: The ability to absorb energy and resist cracks or fractures.
Thermal Conductivity: Good thermal conductivity helps in efficient heat dissipation during the moulding process.
Corrosion Resistance: Some steels are treated or alloyed to resist corrosion, which is important for longevity and maintaining product quality.
Heat Treatment:
Annealing: Softening the steel to improve machinability.
Quenching and Tempering: Hardening the steel and then tempering it to reduce brittleness.
Surface Hardening: Techniques like nitriding can be used to enhance surface wear resistance.
In summary, plastic mould companies play a vital role in the manufacturing sector by creating and maintaining moulds that shape plastic products. The choice of steel used in these moulds is critical, as it affects the mould’s performance, durability, and the quality of the end product.